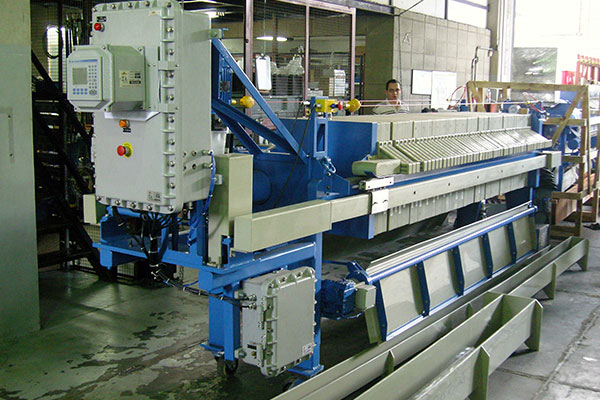
Por dentro da produção de ÓLEO E GÁS - Revista Meio Filtrante
A indústria de petróleo e derivados é considerada, em toda sua extensão, desde a plataforma de exploração às refinarias, referência em tecnologia de ponta, onde os sistemas filtrantes são de grande importância.
Por Tiago Dias
A produção de petróleo é geralmente realizada através de exploração e produção, cujas características variam de acordo com a profundidade da água, a vazão dos poços, as propriedades locais do oceano, a distância do litoral, entre outros detalhes. Para se ter uma idéia, a produção é intensa. Segundo a ANP – Agência Nacional do Petróleo, Gás Natural e Biocombustíveis, o volume de petróleo refinado no Brasil gira em torno de 640 milhões de barris por ano, enquanto a produção nacional do gás natural fica na média de 112 milhões de m3. Conforme informações da Petrobrás – Companhia Integrada de Petróleo, no começo o segmento era bem diferente. Nas primeiras produções marítimas de petróleo no Brasil,
o líquido era retirado em lâminas d’água inferiores a 150 metros, quando se utilizavam plataformas fixas, construídas em terra e posteriormente transportadas por barcaças e navios-guindastes para instalação em pleno oceano. À medida que as descobertas foram atingindo profundidades maiores, a utilização de equipamentos fixos no fundo do mar ficou inviável.
A opção técnica passou a ser as plataformas flutuantes. E é através delas que o petróleo cru é extraído. O gás natural vem associado normalmente ao petróleo e hoje é um sinal de desenvolvimento. Por conta disso, uma plataforma é considerada uma ilha cheia de mecanismos, tecnologias e equipamentos necessários para diversas etapas do processo. Um exemplo são os sistemas filtrantes. Existem vários processos de filtração na indústria do petróleo, os quais são específicos para cada caso. “Além das características técnicas inerentes ao circuito nos quais são instalados, o setor muitas vezes exige certos detalhes como conexões especiais, perda de carga limitada, posicionamento de indicadores de saturação, adequação de indicadores elétricos de saturação para áreas classificadas, garantia de operação da linha sem interrupção de fluxo, entre outros”, observa o Engº Alex Peixoto da Assistência Técnica da Hydac, fabricante de sistemas hidráulicos. A indústria do petróleo e do gás natural compreende diversas etapas, dando início com a pesquisa, exploração e produção. Na seqüência, o transporte, armazenamento, o refino e a comercialização, quando o objetivo é a venda a consumidores externos. No caso do Brasil, por ser a Petrobrás uma companhia integrada, o petróleo sai dos campos e se destina às bases terrestres, as quais, através de um sistema de logística complexo por oleodutos, transfere o petróleo às refinarias adequadas ao perfil do óleo bruto.
Exploração e Perfuração
Os produtos derivados de petróleo são largamente utilizados em quase todos os segmentos de atividade humana. O químico Nelson Roberto Cancellara, da Gerência de Otimização da RECAP – Refinaria de Capuava, em São Paulo, explica suas origens. “O petróleo e o gás natural são encontrados em bacias sedimentares e depressões da crosta terrestre, onde foram se formando há alguns milhões de anos, como produto de decomposição/transformação de microorganismos que se acumularam no local, empregando certo tipo de rocha denominada de “rocha mãe” que, formada por sedimentos de matéria orgânica, é capaz de armazenar imensas quantidades de hidrocarbonetos, desde o petróleo e gasolina natural até frações mais leves de gás”, conta. O ponto de partida nesta busca é a exploração, através de estudos preliminares para a localização de uma jazida e, assim, a identificação do petróleo nos poros das rochas. A perfuração ocorre e locais previamente determinados pelas pesquisas geológicas e geofísicas. Para realizá-la, perfura-se um poço usando um sonda. Comprovada a existência do petróleo, outros poços serão perfurados para avaliar a extensão da jazida. Essa informação é que vai determinar se é comercialmente viável ou não produzir petróleo descoberto.
Produção e Extração
A fase de extração do petróleo começa após a avaliação da extensão da jazida. Em cada poço é introduzida uma tubulação de aço na superfície até o fundo, chamada de revestimento. Conforme informações da Assessoria de Comunicação da Petrobrás, o espaço entre as rochsa perfuradas e o revestimento é preenchido com cimento, para impedir a comunicação entre as várias zonas porosas que foram atravessadas pelo poço. O passo seguinte é descer o canhão pelo interior da tubulação de aço. Essa ferramenta perfura o revestimento e o cimento criando uma comunicação, entre a jazida e o interior do poço. Geralmente, os fluidos que migram da rocha geradora são extraídos através de uma coluna de produção. Os processos de elevação artificial têm como objetivo maximizar
o volume do petróleo a ser extraído. Os mais utilizados na indústria de petróleo são: bombeio mecânico, bombeio por cavidades progressivas, bombeio centrífugo submerso, bombeio hidráulico e elevação pneumática ou gás-lift. Segundo a Petrobrás, a recuperação secundária pode ser realizada por técnicas tradicionais, que são a injeção de água (ou gás) ou através de técnicas mais sofisticadas, como por exemplo, a injeção de gás carbônico e de polímeros, entre outras. Os filtros são importantes nos sistemas de produção de petróleo, principalmente no processo de injeção de água nos reservatórios. Nas plataformas de produção, são utilizados Filtros Cartucho no sistema de injeção de água, com a finalidade de controlar a concentração de petróleo e de sólidos suspensos na água a ser injetada. Como o petróleo está nos poros das rochas, e não em bolsões ou lagos subterrâneos, a injeção de água visa manter a pressão na rocha-reservatório e deslocar o petróleo para os poços. Para evitar o bloqueio dos poros da rocha-reservatório é necessário limitar a concentração de óleo e sólidos presentes na água injetada.
Filtro Separador Centrífugo
Durante o período de produção, há diversos problemas que podem ocorrer devido ao acúmulo de areia no separador de produção, local onde o gás e a água são separados do petróleo. As causas são diversas: redução do tempo de resistência dos separadores de produção, parada de produção total ou parcial para remoção de areia acumulada, abrasão dos internos de válvulas, acessórios, bombas e instrumentos, e até risco de vazamento de óleo por desgaste prematuro de componentes. Para evitar problemas na plataforma, muitas utilizam um Conjunto Separador Centrífugo, constituído de um Filtro Separador Contínuo, um vaso coletor de areia e uma bomba de cavidade progressiva totalmente instrumentada, permitindo a remoção contínua da areia produzida sem a necessidade de se interromper a produção. Segundo a DBD Filtros, fabricante e distribuidora de filtros, o retorno do óleo limpo, no caso de aplicações em separadores de produção bifásico, ou água produzida, no caso de aplicações em separadores de produção trifásicos, se dá utilizando-se a entrada da linha já existente (espinha de peixe), que será substituída por um sistema de bicos redutores, permitindo uma varredura uniforme e sem turbulência do leito do separador de produção. O coletor de sólidos acumula a areia separada, praticamente isenta de líquidos, em bags, permitindo uma remoção rápida e limpa, sem parar o sistema que continua removendo a areia e acumulando no próprio corpo do Filtro Separador Centrífugo. “A aplicação deste sistema proporciona grande redução de custos no processo”, comenta André Luiz Moura, Gerente Geral da empresa.
Refino
O petróleo puro extraído do poço não tem aplicação direta, mas sim, seus derivados. Para que isso ocorra, o petróleo é fracionado em seus diversos componentes através do refino ou destilação fracionada. Na própria plataforma de produção é feita a separação da fase gasosa da líquida. Segundo informações da Petrobrás, o óleo vai para as refinarias onde é convertido em derivados (gasolina, óleo diesel, gás doméstico – GLP, querosene de aviação, óleo combustível, asfalto, coque, nafta – base da indústria petroquímica, entre outros). O gás natural é transportado por gasodutos direto para o consumo, uma vez que é uns produtos finais, prontos para o uso, sem necessitar de maiores tratamentos. Para ser armazenado tem que ser liquefeito. Existem também reservatórios exclusivos de gás, escoado por dutos diretamente para o consumo na indústria como combustível, em residências e nas usinas termoelétricas. O gás também é utilizado como matéria-prima para a indústria petroquímica. É exatamente nesse ponto de refino onde há maior utilização de sistemas filtrantes, principalmente para acabamento de produtos. Os equipamentos empregados nas atividades industriais da Petrobrás, por exemplo, utilizam sistemas que incorporam tecnologia de filtração, onde cada produto obtido no refino depende de uma série de variáveis: da qualidade do petróleo que está sendo processado e da estrutura da refinaria – sua complexidade, unidade e mercado em que atua. “Invariavelmente, fabricamos filtros e vasos atendendo as especificações especiais dos clientes, principalmente da Petrobrás, onde os requisitos de qualidade e exigências para atendimento das condições processuais são bastante rigorosos. As normas usualmente aplicáveis N253, N1706, N1704, N266, N2 e inúmeras Estações de Tratamento, documentos específicos para cada projeto que trazem informações adicionais sobre as condições de processo, materiais, local da instalação, etc.”, exemplifica Décio P. Camargo Filho, Engenheiro de Aplicações da Gascat, fabricante de equipamentos e sistemas destinados ao transporte e à distribuição de gás natural e gases industriais.
Filtro Cartucho
A aplicação dos Filtros Cartucho, por exemplo, pode ocorrer na etapa de acabamento, na remoção de água e contaminantes, como explica Nelson, da RECAP: “Os filtros Cartucho são empregados no tratamento de água de processo, normalmente como macro barreiras, condicionando o fluxo antes da entrada para um processo mais refinado de polimento, onde partículas mais grosseiras, se presentes, causariam baixo rendimento desses sistemas” comenta.
O Engº Edison Ricco Junior, da Apexfil, que fabrica e comercializa filtros industriais, observa que as opções para sua utilização são bem amplas: “Pode-se aplicar em qualquer etapa do processo que se queira obter uma melhor performance do fluido ou proteção de equipamento. Podem reter partículas, gotículas ou qualquer corpo estranho que se queira retirar do processo”, diz. Por conta disso, o filtro pode sofrer algumas variações de acordo com as necessidades, como por exemplo:
• Elemento filtrante com grau de remoção de 4,5 micra;
• Classificação absoluta (segundo NFPA, método ISO-4572 adaptado);
• Eficiência de 99,98%;
• Equivalente a índice Beta 5000, conforme norma ANSI B93.31 de 1973;
• Confeccionado em polipropileno plissado.
Membranas
Membranas filtrantes são utilizadas para o polimento. Podem-se utilizar processos como microfiltração, ultrafiltração, nanofiltração, osmose reversa ou eletrodiálise. A técnica ou processo é escolhido para atender aos requisitos da especificação da água permeada em questão, levando-se em conta também o custo do empreendimento. Veja, na próxima página, a relação das técnicas de filtração por membranas e dados comparativos entre elas. Além do uso em polimento de água, a filtração por membrana é muito difundida também para separação de um determinado componente de uma mistura gasosa. Tais aplicações são específicas e não necessariamente custosas, porém, proporcionam um rápido retorno do capital empregado.
Filtros especiais e de processos
Nas refinarias também são utilizados regularmente filtros de tela nas sucções das bombas e outros tipo de filtros especiais em diversos tipos de processo, como na produção de parafinas, em soluções para tratamento de gases, entre outras aplicações. Segundo Maurício Biral, da Engenharia de aplicações da Tech Filter, os filtros de sucção são fabricados com malha grosseira para reter eventuais peças soltas, como por exemplo, parafusos, protegendo assim a bomba. Maurício também comenta sobre os Filtros Cesto: “Às vezes, são conhecidos também como filtros de tela, semelhante aos de sucção, filtros grosseiros, contra eventuais partículas da linha”, comenta. Ambos são séries especiais que possuem características construtivas e de performance, conforme a necessidade exigida, sendo capaz de atender as normas internacionais relacionadas ao processamento do petróleo e seus derivados. “Como características de maior destaque estão as opções construídas em aço inoxidável e faixas de pressão, indo desde a aplicação como filtros de sucção até situações com pressões de 1000 bar”, esclarece Alex Peixoto, da Hydac. Já os filtros de processo também estão disponíveis em uma diversidade bem ampla de opções, muitas vezes utilizando um meio filtrante diferente, desde os com grande abertura para filtração grosseira, até o grau de retenção absoluto, utilizando diferentes materiais construtivos, como exemplifica Alex: “No caso dos filtros de processo, podemos citar desde os modelos mais simples, utilizando cartuchos descartáveis ou laváveis manualmente, indo até os modelos auto-limpantes retrolaváveis, que permitem vazão permanente oferecendo baixíssima perda de carga”. Entretanto, os filtros de processo para fluidos são utilizados para a retirada de uma massa muito grande de contaminantes, ou para garantir que em uma única passagem sejam retidos todos os contaminantes acima de um determinado tamanho.
Filtros Hidráulicos
Filtros de aplicação hidráulica e de proteção de sistemas de lubrificação são aplicados em praticamente qualquer tipo de circuito, inclusive aqueles que possuem características específicas ao setor como aplicações off-shore, submarinas, em áreas classificadas, entre outras. “Os filtros hidráulicos e de lubrificação, forçada a óleo são utilizados de limpeza do fluido hidráulico ou lubrificante em circuitos que utilizam normalmente óleo de base mineral, podendo haver aplicações especiais com fluídos sintéticos, porém com o mesmo objetivo de limpeza”, explica Alex.
Soluções para gases
O gás é filtrado praticamente em todo o processo produtivo, podendo ser utilizados filtros coalescentes ou mesmo algum outro filtro, como tipo cesto com malha fina para retenção de particulados. “Filtros coalescentes são usados para ar comprimido e gases em geral, para a retenção de particulados e, principalmente, para remover óleo e água”, explica Maurício, da Tech Filter. Na exploração, o gás é separado do óleo, hidrocarbonetos e água que se apresentam nesta fase da produção. Após isso, segundo o Engº Décio, da Gascat, o gás é novamente tratado visando a separação mais fina e preparando-o para o transporte. “durante o processo de transporte, o gás é bombeado e filtrado continuamente, visando a retirada de hidrocabonetos e óleo lubrificante injetado pelo processo de compressão (filtros coalescente). Nos city Gates o gás sofre mais um tratamento de filtração, com filtros combinados ciclone e cartucho separadores, visando a adequação do mesmo para a etapa de regulagem e medição”, explica. Finalmente, durante a distribuição ao usuário, o gás é normalmente filtrado e tratado antes do consumo final.
Filtro prensa
Na extração de petróleo, em alguns casos utilizam-se filtros prensa para a filtração do produto in natura, removendo desta forma os sólidos em geral arrastados nesta operação, antes do mesmo seguir para os próximos passos de beneficiamento industrial. “Pode estar presente no fluxo produtivo desde a entrada da matéria-prima, processos de manufatura e beneficiamento intermediários (por exemplo, garantia de isenção de particulados no envase)” explica Renato Marne, Gerente Industrial da Tecitec. A filtração do óleo ou seus insumos, pode ser realizada sempre que houver a necessidade de remoção dos sólidos presentes e indesejáveis ao processo seguinte ou mesmo do produto final. “É bastante aplicada durante o processo de preparação e acabamento, onde há mistura de insumos como aditivos, adsorventes, sequestantes, adicionados ao óleo na forma de sólidos ou também possíveis sólidos originados durante as reações químicas para a preparação do produto, os quais devem ser removidos”, diz Renato. A diferença é que em virtude dos processos requeridos nas indústrias, muitas vezes o produto tem que ser filtrado em temperaturas elevadas, requerendo, portanto, placas especiais confeccionadas em alumínio, ferro fundido ou até mesmo aço inoxidável. Os elementos filtrantes, por ua vez, também são confeccionados com tecidos técnicos especiais e, em muitos casos, utiliza-se o papel como elemento filtrante.
Produtos Acabados
Quando os produtos saem do processo de acabamento, é necessário certificar se os mesmos estão dentro das especificações de qualidade com relação ao teor de contaminantes, já que alguns deles, tais como gasolina, diesel querosene e gasolina de aviação, óleo combustível, são, na realidade, uma mistura de vários lotes produzidos nas diferentes unidades da refinaria. Há remoção de particulado sólido no produto acabado também, conforme conta Edson P. Castro, Executivo de Vendas da 3M/Cuno, fabricante de filtros para o segmento: “Dessa maneira, garante-se a qualidade final sem a necessidade de reprocessamento, além de reduzir os problemas causados por incrustações nos equipamentos de distribuição que provocam a necessidade de manutenção freqüente e alto custo de reparo”.
Tratamento de Água
Água Industrial: Como qualquer outra planta industrial, as plataformas, refinarias e todas as indústrias do segmento tratam águas e efluentes. Os filtros aparecem inicialmente na pré-filtração das águas industriais. Segundo Edson, os elementos instalados podem ser fabricados com polipropileno ou celulose. “Os filtros bags e cartuchos são instalados em série para reduzir a quantidade de material particulado, garantindo a qualidade de água para a proteção da osmose reversa, das colunas de troca iônica ou dessalinizadores: diminuindo o consumo e o custo de produtos químicos e mão de obra com a limpeza, reduzindo o make-up de resina” explica. Água Injeção: Como já visto, hás também o tratamento da água para injeção nos poços de petróleo, onde são utilizados filtros cartucho de 5 micra High Flow, conforme conta Edson. “O principal objetivo é a filtração, proteger a formação da obliteração por material particulado, o que impediria, com o tempo, a injeção de água e, conseqüentemente, a produção de petróleo, minimizando o número de intervenções nos poços de injeção para limpeza por ataque químico e/ou térmico da formação, além de evitar o faturamento da formação por entupimento dos poros”, esclarece. Segundo informações da Petrobrás, os processos para o tratamento de água variam conforme o uso a que se destina. Por exemplo, para água de refrigeração usa-se a clarificação (geralmente utiliza-se filtro de areia) e a cloração, já para a água de caldeiras faz-se também a desmineralização com resinas trocadoras de íons ou por osmose. Quanto aos efluentes, os tratamentos se classificam em primário (remoção de óleos e graxas em separadores mecânicos tipo API e flotadores), secundários (biodigestão aeróbica) e terciários (filtração em carvão ativo, em casca de nozes, etc). A escolha do conjunto de sistemas é feita levando-se em conta a qualidade e vazão do efluente, o corpo receptor e a legislação do local. Em termos de reuso, há a água de processo, usada nas etapas de dessalgação do petróleo e lavagem de gases.
Distribuição e Comercialização
A atividade de distribuição engloba a aquisição, armazenamento, transporte, comercialização e o controle dos combustíveis.
A empresa responsável por esta atividade é a subsidiária Petrobrás Distribuidora, que mantém um rigoroso sistema de controle de qualidade: o programa De olho no Combustível. O caminho para o óleo e gás chegarem ao comércio é comprido, mas muito bem amparado por equipamentos como sistemas de filtração, para que cada etapa do processo seja realizada com eficácia e qualidade.
Fonte: Matéria publicada na Revista Meio Filtrante, Ano VII, nº 34, Setembro/Outubro de 2008, páginas 10 a 17